3 Factors of Target Quality Influence Large-area Coating
- surftech22
- Feb 3, 2023
- 3 min read
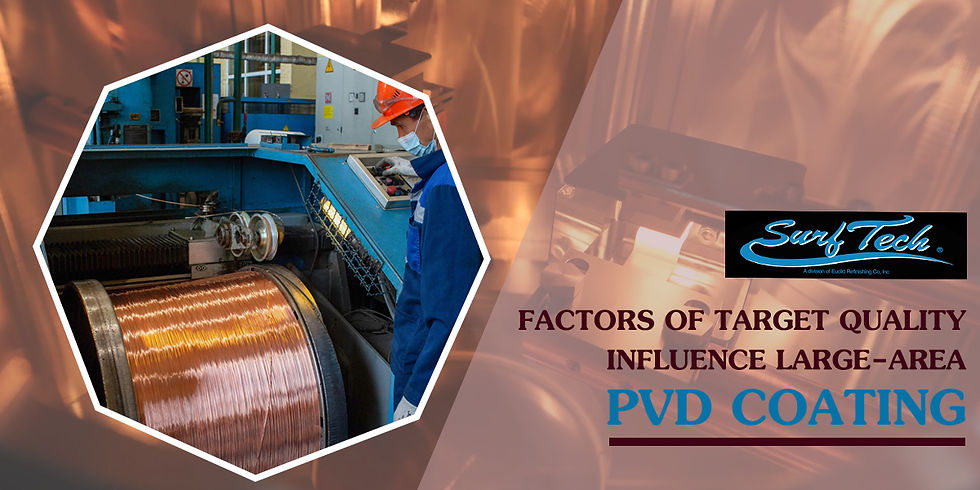
Most modern buildings have begun to use large areas of glass for lighting, which has the advantage of providing us with brighter light and a wider view. However, because the heat energy transmitted through the glass is much greater than that transmitted through the surrounding walls, the overall energy consumption of the building increases significantly. To address this issue, researchers have begun to investigate and implement large-area Low-E glass.
Low-E glass is widely used in building construction due to its ability to save energy, control light, and be aesthetically pleasing. Because sputtering target material is an important component in the production of low-E glass, this article will discuss three target quality factors that influence large-area copper PVD coating of low-E glass.
The Shape of The Target Materials
According to their shapes, planar targets and rotatory targets are commonly used for large-area coating. The target's shape influences the stability and film properties of the magnetron sputtering coating, as well as the target's utilization rate. As a result, changing the shape design of the target can improve coating quality and production efficiency while saving money.
Relative Density & Porosity of The Target
The target's relative density is the ratio of its actual density to its theoretical density. The theoretical density of a single-component target is the crystal density, and the theoretical density of an alloy or compound target is calculated by multiplying the theoretical density of each component by the proportion of the alloy or mixture.
If the target material is loose and porous, it will absorb more impurities and moisture, which are the primary sources of pollution during the custom PVD coating process. These impurities will slow down the acquisition of high vacuum, cause electrical discharge during the sputtering process, and even burn out the target.
Target Grain Size And Crystallographic Direction
The target with the smaller grain size has a faster deposition rate for targets of the same composition. This is primarily because grain boundaries are more vulnerable to attack during the sputtering process, and the more grain boundaries there are, the faster the film forms.
Furthermore, the grain size influences the quality of the film formation. For example, in the Low-E glass manufacturing process, NiCr thin-film is used as the protective layer of the infrared reflection layer Ag, and its quality has a significant impact on the coating products. Because the NiCr film has a relatively high extinction coefficient, it is typically plated very thinly (about 3nm). The compactness of the film will be poor, the protective effect of the Ag layer will be reduced, and the coating product will be oxidized and removed if the grain size is too large and the sputtering time is too short.
Conclusion
The shape of the target has the greatest influence on the target material's utilization rate, and a reasonable size design can improve the target material's utilization rate while saving money. The smaller the grain size, the faster the coating rate and the more uniform the coating. The higher the purity and density, the lower the porosity, the better the film formation quality, and the lower the likelihood of slag removal by discharge.
SurfTech INC is capable of selecting and implementing the best stainless steel product for you, and we provide Assisted PVD coating, thin film coating, and ceramic coating facility in the United States. Contact us today for a quote, to learn more about our process, you can call us on +1-440-275-3356 and email us on ncotton@ercsurftech.com.
Original Source,https://bit.ly/3JDgj3b
Comments