Step-by-Step Guide to PVD Coating Process
- surftech22
- May 21, 2024
- 3 min read
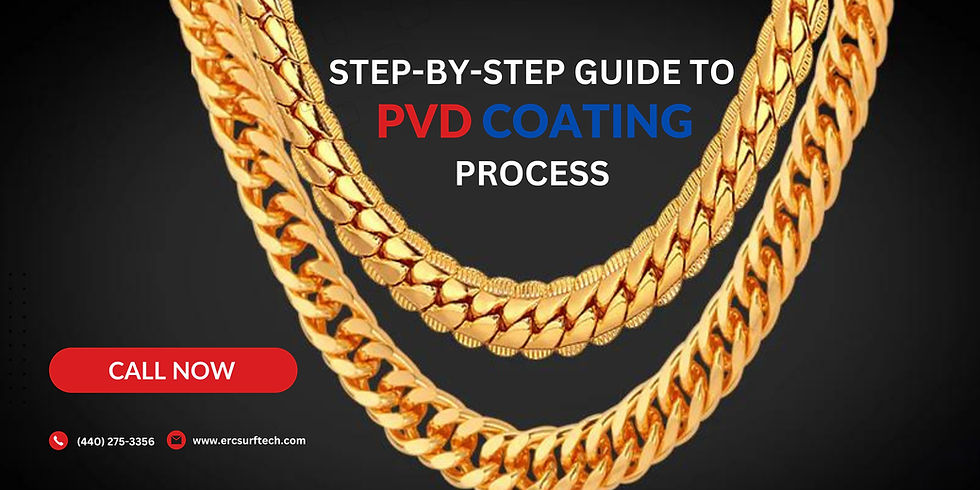
Physical Vapor Deposition (PVD) is a cutting-edge technology used for applying thin films to various surfaces. This PVD Coating Process is widely employed in different industries, from electronics to automotive, due to its numerous advantages such as durability, resistance to corrosion, and aesthetic appeal. This guide will provide a comprehensive overview of the PVD Coating Process, detailing each step involved, its benefits, and why choosing a specialized service like ercsurftech.com is advantageous.
Understanding PVD Coating
What is PVD Coating?
PVD Coating is a vacuum deposition method that involves the transfer of material from a condensed phase to a vapor phase and then back to a thin film condensed phase. This technology is renowned for producing coatings with superior hardness, low friction, and high resistance to corrosion.
Applications of PVD Coating
PVD coatings are utilized in a variety of sectors, including:
Automotive: Enhancing the durability and appearance of components.
Aerospace: Protecting parts against extreme conditions.
Medical: Coating instruments for biocompatibility and longevity.
Electronics: Improving the wear resistance of components.
Step-by-Step Guide to the PVD Coating Process
Step 1: Surface Preparation
The first crucial step in the PVD Coating Process is surface preparation. This involves:
Cleaning: Removing contaminants such as oil, dirt, and rust to ensure proper adhesion.
Polishing: Smoothing the surface to enhance the quality of the coating.
Step 2: Loading into the PVD Chamber
After preparation, the items to be coated are placed into the PVD chamber. This environment is tightly controlled to maintain the purity of the coating process.
Step 3: Vacuum Creation
The chamber is then evacuated to create a vacuum. This step is essential to:
Prevent Contamination: Ensuring the coating material does not react with air or other gases.
Control Coating Properties: Achieving the desired thickness and uniformity.
Step 4: Heating the Substrate
The substrate, or the surface to be coated, is heated to a specific temperature. This enhances the bonding strength between the coating material and the substrate.
Step 5: Vaporization of the Coating Material
The coating material, often a metal or ceramic, is vaporized. This can be done using various techniques such as:
Thermal Evaporation: Heating the material until it vaporizes.
Sputtering: Bombarding the material with high-energy particles to release atoms.
Step 6: Deposition
The vaporized coating material travels through the vacuum and deposits onto the substrate, forming a thin film. The deposition rate and thickness are meticulously controlled to meet specific requirements.
Step 7: Cooling and Unloading
Once the coating is applied, the substrate is allowed to cool. After cooling, the coated items are removed from the chamber, inspected for quality, and prepared for use.
Benefits of PVD Coating
Durability and Wear Resistance
PVD coatings significantly enhance the durability and wear resistance of surfaces, making them ideal for applications subject to high stress and friction.
Corrosion Resistance
These coatings provide excellent protection against corrosion, extending the lifespan of components exposed to harsh environments.
Aesthetic Appeal
PVD coatings can be tailored to achieve various colors and finishes, improving the visual appeal of products.
Environmental Friendliness
The PVD Coating Process is environmentally friendly, producing minimal waste and avoiding the use of harmful chemicals.
Why Choose Us
Choosing the right PVD coating service provider is crucial for ensuring high-quality results. Here’s why ercsurftech.com stands out:
Expertise: Extensive experience and knowledge in PVD coating technology.
Advanced Equipment: State-of-the-art machinery ensuring precision and quality.
Customization: Tailored solutions to meet specific client requirements.
Quality Control: Rigorous inspection processes to guarantee top-notch coatings.
Sustainability: Commitment to environmentally friendly practices.
Conclusion
The PVD Coating Process is a sophisticated technology that offers numerous benefits, including enhanced durability, corrosion resistance, and aesthetic improvements. For industries seeking top-quality PVD coatings, partnering with a reputable provider like ercsurftech.com ensures exceptional results. With their expertise, advanced equipment, and commitment to quality, ercsurftech.com is your go-to source for all your PVD coating needs.
For more information or to get started with your PVD coating project, visit ercsurftech.com today.
Reference URL :- Step-by-Step Guide to PVD Coating Process
Comments